In the ever-evolving landscape of semiconductor technology, the journey from raw silicon wafers to the compact, powerful chips within our smartphones involves a crucial step known as “packaging.”, which in recent days have evolved to advanced packaging. This process, once considered an afterthought, has undergone a revolution in recent years. Advancements in packaging technologies have become instrumental in the pursuit of smaller, more powerful, and higher-performing semiconductor devices.
In this blog post, we’ll explore the fascinating world of advanced packaging, including wafer-level packaging, bumping, redistribution layers, fan-out, and through-silicon vias.
Join Our WhatsApp News for updated information on semiconductors & AI
1. Wafer-Level advanced Packaging (WLP): Frosting the Whole Cake
Traditionally, semiconductor packaging involved cutting up finished wafers into individual chips, which were then encapsulated.
Wafer-level packaging (WLP) takes a different approach by packaging the die while it is still on the wafer. This innovative technique involves bonding protective layers to the top and/or bottom of the wafer, establishing electrical connections, and subsequently dicing the wafer into individual chips.
WLP, likened to frosting an entire cake before slicing it, offers advantages like smaller chip size and streamlined manufacturing.
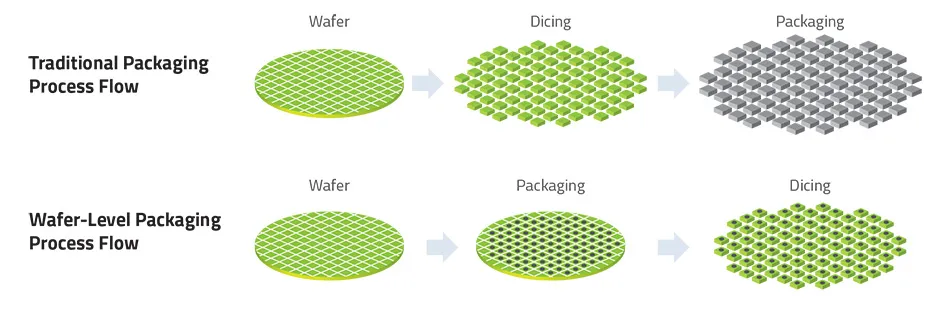
Analogy:
Imagine conventional packaging as frosting individual cupcakes, each chip treated separately after being cut from the wafer. Now, envision wafer-level packaging (WLP) as a baker frosting an entire cake before slicing it into pieces.
Protective layers are bonded to the top and/or bottom of the wafer, establishing electrical connections. The wafer is then diced into individual chips using a “cake frosting” approach. This results in smaller chip sizes and streamlined manufacturing, similar to preparing a complete dessert before serving.
Read More: What is 2D, 2.5D & 3D Packaging of Integrated Chips?
2. Bumping and Flip Chips: Small Balls with Big Connections
Bumping, a crucial step in semiconductor packaging, involves creating small conductive balls, or bumps, on the chip’s surface. These bumps enable a simplified electrical connection between the chip and the circuit board.
In the flip chip bonding process, the bumped die is flipped upside down, aligning the bumps with corresponding pads on the board. This method provides benefits such as a smaller package size and increased device speed.
Various materials, including solder, gold, copper, or cobalt, can be used for bumping, each catering to specific applications.

Analogy:
In the world of semiconductor packaging, the bumping process is like equipping a chip with tiny, electrically conductive balls—think of them as the chip’s personalized arsenal.
These bumps, when strategically placed, create a simple yet effective electrical connection.
Imagine a flipped chip as a skilled archer hitting bullseyes by aligning its bumps with targets on the circuit board. This precise flip chip bonding results in advantages like a smaller package size and increased device speed.
3. Redistribution Layers (RDL) advanced Packaging
Redistribution layers (RDL) play a pivotal role in efficiently relocating contact points on the wafer. By rerouting connections using a dielectric film and metal lines, the original bond pads can be redistributed to desired locations.
This “fan-in” process not only enables higher contact density but also results in one of the smallest package sizes available. The addition of underbump metallization layers supports the subsequent soldering process.

Analogy:
Consider the semiconductor wafer as a bustling city with traffic flowing through predefined routes. Now, imagine redistribution layers (RDL) as urban planners rerouting traffic to ease congestion.
The RDL process creates new paths for connections by depositing dielectric films and metal lines, enabling higher contact density and efficiency. This “urban planning” of electronic connections through RDL leads to one of the smallest package sizes available, similar to optimizing city layouts for improved traffic flow.
Read more: U.S. launches $3 billion Program for Advanced Semiconductor Packaging
4. Fan-Out Wafer-Level Advanced Packaging (FOWLP): Spreading Connections for Efficiency
The redistribution process can be further leveraged in fan-out wafer-level packaging (FOWLP) to spread or “fan out” connection points beyond the chip’s dimensions.
This is particularly useful when the chip shrinks in size while requiring the same number of contact points. FOWLP involves dicing the front-end-processed wafer into individual die, spacing them on a carrier structure, and redistributing contacts using WLP processing.
The result is improved electrical and thermal performance, along with a reduction in overall package height.

Analogy:
Picture a chip as a bustling neighborhood, where houses (individual chips) are spaced out with sufficient gaps. Fan-out wafer-level packaging (FOWLP) acts as a city planner deciding to spread the houses beyond their original positions.
FOWLP enhances electrical and thermal performance by dicing the wafer, spacing individual die on a carrier structure, and redistributing connections beyond the chip’s dimensions. It’s similar to reorganizing a neighborhood layout for improved community dynamics.
Read More: What are the Various Types of Semiconductor Packaging
5. Through-Silicon Vias (TSVs): Efficient Chip Stacking
To optimize space on a circuit board, one can stack chips using through-silicon vias (TSVs). TSVs establish the shortest path through a chip’s entire thickness by etching holes and filling them with conductive materials like copper. This enables stacked assemblies with improved electrical performance, lower power consumption, and greater bandwidth.

Analogy:
Think of traditional chip stacking with wire bonding as building a skyscraper using external elevators. Now, imagine through-silicon vias (TSVs) as installing secret tunnels within each floor, enabling direct connections between different levels.
TSVs, or Through-Silicon Vias, traverse the chip’s entire thickness, establishing the shortest path from one side to the other. Like a hidden network optimizing efficiency in a multi-level building, TSVs enable efficient chip stacking, leading to improved electrical performance, lower power consumption, and increased bandwidth.
Read More: 3 Course to Master Chip Packaging from Basic to Advanced in 24 hours
Advanced Packaging techniques Comparison
Technology | Analogy | Key Characteristics | Companies Involved |
---|---|---|---|
Wafer-Level Packaging (WLP) | Frosting the Whole Cake | – Protective layers and electrical connections applied to entire wafer. – Smaller chip size. – Streamlined manufacturing. | – ASE Group – Amkor Technology – STATS ChipPAC |
Bumping and Flip Chips | Small Balls with Big Connections | – Electrically conductive bumps on the chip. – Flip chip bonding for smaller package size and increased device speed. | – Intel – AMD – TSMC – Samsung |
Redistribution Layers (RDL) | Rerouting Connections for Efficiency | – Rerouting contact points using dielectric films and metal lines. – Higher contact density. – Efficient use of space. | – ASE Group – Amkor Technology – JCET (Jiangsu Changjiang Electronics Technology) |
Fan-Out Wafer-Level Packaging (FOWLP) | Spreading Connections for Efficiency | – Dicing wafer into die, spreading them, and redistributing connections. – Improved electrical and thermal performance. | – TSMC – Amkor Technology – STATS ChipPAC |
Through-Silicon Vias (TSVs) | Efficient Chip Stacking | – Electrical connections through the entire thickness of the chip. – Enables efficient chip stacking with improved performance. – Lower power consumption and greater bandwidth. | – Intel – TSMC – Samsung – GlobalFoundries |
Advanced Packaging Technology Evolution: From Afterthought to Innovation Hub
The once-overlooked packaging phase in semiconductor manufacturing has evolved into a hub of innovation and complexity.
Wafer-level packaging, with its advancements in materials, processes, and equipment, stands out as one of the fastest-growing chip packaging technologies.
Bumping, redistribution layers, fan-out, through-silicon vias, and other techniques work together to create compact, powerful chips for our mobile devices. These technologies play a crucial role in achieving high-speed functionality, a defining feature of modern semiconductor devices.
Looking ahead, leading-edge packaging technologies will be even more vital for the next generation of semiconductor devices.